About
See our full range of yarns
YarnsThe Beginnings
From 1979, when the first Angora goat was purchased, the family passion for Angora goats has carried on through to the present day, with almost 2,000 goats reared and cared for at Wagtail Yarns farm. The journey from the past to the present has been a long, and at times challenging one, however one that Betty, Kevin and Gaylene have been through together, and one that has taken them across continents in a bid to produce some of the finest pure Kid Mohair in the world.
Wagtail Yarns is an amalgamation of two past family farms and businesses, where the Angora goats were initially bought to control scrub growth. As the herd grew, the family identified an opportunity to add value to the goats and so in 1986, they started to spin and process the mohair with some outside involvement, ready to be knitted at the farm into warm bulky durable mohair garments. Not long after, a decision was taken to completely process the fibre on the farm, cutting out any third party involvement – giving them greater control over the quality of production. The result from deciding to do it all themselves is, apart from all the other yarns, a very fine soft durable laceweight 100% (definitely no synthetic) kid mohair yarn that is sought after around the world.
In 1995, Wagtail Yarns was registered as a new business run between Betty, Kevin and Gaylene in Childers, Queensland taking over from the previous business of Wallum Yarns.
Machinery has been purchased and imported over the years from England, South Africa, Germany, Italy and the US – but not without complication. The first of many challenges that the business has faced. Some challenges are enjoyable. At times we have not been able to source the machinery that we have needed and so we have created / developed / engineered what we needed. And while the resulting machine may not look beautiful, it gets the job done.
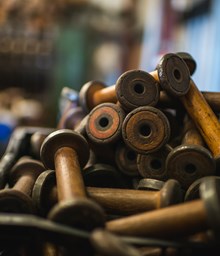
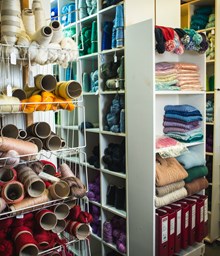